What is Hot-in-Place Asphalt Recycling Technology?
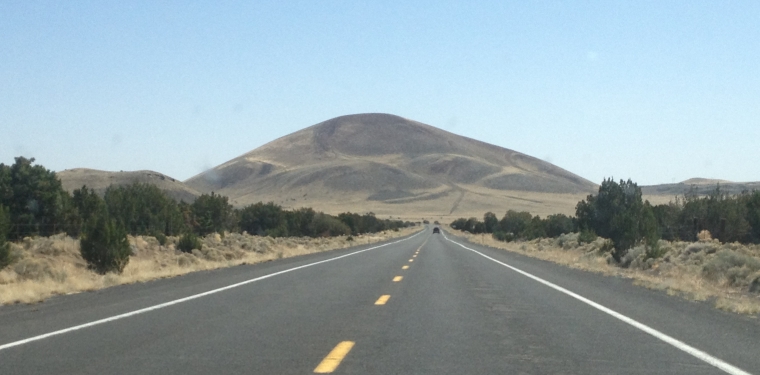
Hot-in-place asphalt recycling technology is not a new method to rebuilt roads. In fact, it has been around for more than six decades, yet despite its many benefits, it is only employed in minimal circumstances as only a handful of municipalities use the technology to repair and repave roadways. The idea, however, has begun to gain traction because of its money-saving aspect as well as its benefits to the environment.
What is the Process?
Hot-in-place recycling (HIR) can be done in three different ways: surface recycling, surface repaving and surface remixing. Recycling involves taking off the top one to two inches of asphalt and then reapplying and compacting it. An overlay of new hot-mix asphalt or another surface treatment goes on top. Surface repaving also involves the same amount of pavement, but only uses a new hot-mix layer atop the recycled layer that is compacted with only one pass of equipment. Remixing combines old and new asphalt with various additives. The roadway is compacted after the mixture is applied.
Numerous Benefits
One of the biggest benefits is that HIR uses up to 35 percent less energy than conventional paving, and reduces the amount of asphalt needed by up to 50 percent. By using less energy and reducing the carbon footprint by releasing fewer greenhouses gases, HIR is a step toward sustainability in road paving. The liquid binding agent used in the process is the only new substance introduced in the process.
This method also minimizes lane closures and spare motorists the risk of driving on half-finished roads with uneven lanes and construction materials and rocks that could end up flying up from the surface and damaging vehicles. The process only adds about an inch to the surface of the roadway, thus allowing the placement of more repair overlays before complete reconstruction must be done.
Used Only in Limited Situations
Despite its benefits, HIR hasn’t caught on with state departments of transportation because of durability issues, but most of those occurred when the roadway surface wasn’t prepared properly. Its usage also has restrictions that include the air void content of the existing asphalt binder. Pavements that have already been heavily patched, have deep ruts or chip-sealed don’t fare well with HIR. Among the states that have approved the process are Illinois, Indiana, Iowa, Wisconsin, Ohio, Michigan, Missouri, Maryland, Tennessee, New Jersey, Oregon and Washington.
Perhaps the biggest benefit of hiR is that it reduces the carbon footprint that road construction places on the environment. HIR can:
- Fill ruts and holes
- Preserve elevations and overhead clearances
- Levels pumps and uneven surfaces
- Re-establishes the surface crown and drainage
Because this technology doesn’t require the manufacture of new asphalt, it’s also helping to reduce the shortage of sand, which has begun to reach critical levels worldwide. We’ll examine that problem in another article that addresses the global sand shortage.